What Makes a Banarasi Saree Unique?
Banaras, also known as Varanasi, is considered a special city for several reasons. Firstly, it is one of the oldest continuously inhabited cities in the world, with a history that dates back over 3,000 years. Secondly, it is regarded as a holy city in Hinduism, Jainism, and Buddhism, and is home to many important temples, including the Kashi Vishwanath Temple, one of the most sacred temples in India. Thirdly, Banaras is renowned for its rich cultural heritage, with a long tradition of music, dance, and literature. Many renowned artists and scholars have called Banaras their home over the years. Lastly, the city is famous for its exquisite textiles, particularly the Banarasi sarees, which are handwoven with intricate designs and considered among the finest sarees in India.
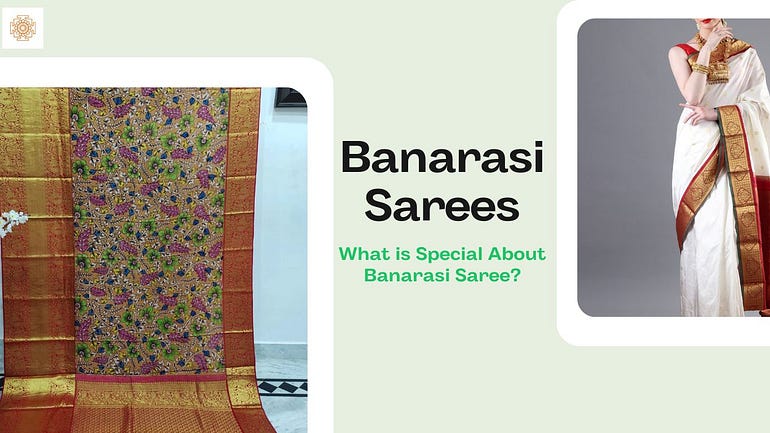
The Banarasi fabric is renowned for its radiant textures, stunning brocades with engraved-like patterns, jewel-toned colors, and splendid zari highlights that embody centuries of cultural richness. These fabrics are unmatched due to their origin on hand-looms, with the rarest versions being entirely hand-woven. As a result, they have become a cornerstone of India’s handloom industry. The intricate weaving process, high-quality raw materials, and secretive techniques used in producing Banarasi fabrics make them highly valuable and exquisite. Nowadays, brocades and Banarasis are made using various base materials and innovative techniques, including power-looms, which reduces costs for customers who prefer the newer versions over the old-world charm of the hand-woven beauties.
Banarasi Sarees are an essential part of the wedding trousseau for most Indian brides due to their cultural significance and grandiose appearance. Typically, the bride wears at least one Benarasi saree during the wedding functions, and in some cases, it may be the reception saree or a special gift from the in-laws. These sarees hold immense value and are seen as a symbol of class and economic status. Banarasi brocades, which are believed to have originated from royalty, have traveled through time and various lands, making them even more prized. The pure silk Banarasi fabric is known as Katan silk, which is usually made without zari borders but with the softest and heaviest silk. They are renowned for their sturdiness and purity, and various types of brocading or designing can be done on this beautiful fabric. Butis, or scattered leaf/floral motifs, are quite popular and are made using Resham or Zari or the Meenakari designs. However, making expensive Banarasi Katan brocades requires an extremely time and labor-intensive technique.
The Rich Legacy of Banarasi Sarees: A Historical Journey
The history of weaving in Banaras is not completely clear. Buddhist records suggest that Varanasi was a significant center for cotton weaving, while other sources mention the production of Hiranya fabric, made of gold, similar to the Kinkhab brocades of Banaras. The city is also mentioned in the Mahabharata, and British records indicate that Banaras was an important weaving center whose brocades were even exported to Europe. While early brocades featured Rajasthani and Hindu motifs, these designs disappeared around the 16th century. Banaras developed into a silk weaving industry in the 17th century, brought to the city by Muslim weavers from Gujarat. The Benarasi weave we see today is influenced by Persian, Mogul, and Central Asian styles, and features motifs like buttis, paisley, jhallar, bel, and Shikargah. Banarasi handloom textile weaving is now one of the largest cottage industries in India, spread across various cities and towns in Uttar Pradesh.
To be specific, the history of the Banarasi saree dates back to ancient times, with some evidence suggesting that Varanasi was a prominent cotton growing and weaving center as early as the 5th century BC. The Buddhist Jataka tales also mention Varanasi as a center of cotton weaving. Banaras has been an important center of weaving since the Vedic period, with the Rig Veda mentioning the production of fabrics made of gold. The production of silk in Banaras began in the 14th century, when Muslim weavers from the neighboring state of Gujarat migrated to the region. These weavers brought with them their skills and expertise in the production of silk fabrics, and Banaras quickly became a hub of silk weaving. The Mughal emperors, particularly Akbar, were known to be patrons of Banarasi silk and played a significant role in the growth of the industry.
Banarasi silk weaving reached its zenith during the Mughal era, when intricate designs and motifs, influenced by Persian, Turkish, and Central Asian cultures, were introduced. These designs included butti (small floral motifs), kalga (paisley motifs), and jhallar (a flowing vine-like pattern), among others. The sarees were often woven with gold and silver threads, and were highly valued and sought after. Over time, the designs and motifs used in Banarasi sarees evolved to incorporate more regional and indigenous elements. The weaving process itself also underwent changes, with the introduction of power looms and other mechanized equipment. However, despite these changes, the Banarasi saree has retained its status as a symbol of luxury, elegance, and tradition, and continues to be highly prized by women across India and around the world.
The Intricate Art of Crafting Banarasi Sarees: A Step-by-Step Guide to the Handloom Weaving Process
Banarasi sarees are intricately crafted handloom sarees that are highly valued for their beauty, quality, and cultural significance. The process of making Banarasi sarees involves several steps, each of which is performed by highly skilled artisans who have been trained in the traditional techniques of Banarasi handloom weaving.
1. The first step in the process is selecting the raw materials. Banarasi sarees are typically made from fine silk, although other materials such as cotton and georgette may also be used. The silk is sourced from different parts of India, and it is important to select high-quality silk that is strong, smooth, and lustrous.
2. Once the silk has been selected, it is washed and prepared for weaving. The process of preparing the silk involves degumming, which removes the natural gum from the silk fibers, and then boiling the silk to improve its strength and durability.
3. Next, the silk is dyed in the desired color using natural or synthetic dyes. The dyeing process is a crucial step in the making of Banarasi sarees, as it determines the final color and appearance of the saree.
4. After the silk has been dyed, it is ready for weaving. Banarasi sarees are typically woven on handlooms, although power looms may also be used. Handloom weaving is a time-consuming and labor-intensive process that requires great skill and attention to detail.
5. The weaving process involves interlacing the warp and weft threads to create the intricate patterns and designs that are characteristic of Banarasi sarees. The patterns may be created using different weaving techniques, including brocade, zari, and butidar.
6. Once the weaving is complete, the saree is sent for finishing. Finishing involves trimming the edges, adding the border and pallu (decorative end piece), and adding any additional embellishments such as sequins, beads, or embroidery.
7. Finally, the saree is washed, ironed, and packed for sale. Banarasi sarees are highly prized for their beauty, quality, and craftsmanship, and they are a cherished part of Indian cultural heritage.
Exploring the Different Types of Banarasi Sarees: A Guide to the Finest Handloom Weaves from India
There are several types of Banarasi sarees, each with its unique characteristics and weaving techniques. Here are some popular types of Banarasi sarees:
● Katan Banarasi Saree — made of pure silk without any mixture of other fibers, this saree is known for its fine texture and durability.
● Organza Banarasi Saree — made of silk and organza, this saree has a sheer, lightweight texture and is often embellished with intricate designs.
● Georgette Banarasi Saree — made of silk and georgette fabric, this saree is known for its elegant drape and flowy texture.
● Shattir Banarasi Saree — made of silk and cotton, this saree has a slightly rough texture and is often used for making everyday wear sarees.
● Tanchoi Banarasi Saree — known for its unique weaving technique, this saree is made of silk and has a satin-like finish with small buti designs.
● Cutwork Banarasi Saree — featuring intricate cutwork designs, this saree is made of silk and often has gold and silver threadwork.
● Jangla Banarasi Saree — known for its floral and vine designs, this saree is made of silk and often has zari work and metallic embroidery.
● Tissue Banarasi Saree — made of silk and golden thread, this saree has a sheer, lightweight texture and a luxurious sheen.
Key Takeaways
1. Banarasi sarees are a type of handloom saree made in Varanasi, India and are known for their intricate designs, luxurious fabrics, and cultural significance in Indian weddings and festivals.
2. The history of Banarasi sarees can be traced back to ancient times and has been influenced by various cultures and traditions over the centuries.
3. The process of making Banarasi sarees involves several labor-intensive steps, including dyeing, warping, weaving, and finishing, and the final product can take weeks or even months to complete.
4. There are several types of Banarasi sarees, including pure silk Katan sarees, georgette sarees, organza sarees, and shattir sarees, each with their own unique characteristics and designs.
5. Banarasi sarees are not just a fashion statement but also a symbol of cultural heritage and craftsmanship, and their popularity continues to grow both within India and internationally.
Comments
Post a Comment